Why forestry mulchers matter in the U.S.
They’ve become the go-to piece of equipment for land clearing. They are deployed for vegetation management across the U.S, from the dense woodlands of the Pacific Northwest to the brushlands of Texas, to the diverse terrains of the Southeast.
These machines have field-proven reliability and adaptability. They provide tremendous efficiency to contractors, public agencies, and private landowners who address needs ranging from simple trail maintenance to complex fire mitigation projects.
Compared with outdated clearing methods, forestry mulchers provide more precise results with lower impact, promoting operations efficiency along with land management.
Method | Efficiency | Environmental Impact | Cost |
---|---|---|---|
Forestry Mulching | High—1-2 acres/day | Minimal, retains soil & roots | High up-front/rent |
Bulldozing | Moderate | High, disturbs soil | Equipment, labor |
Burning | Variable | Air pollution, fire risk | Permits, prep |
Forestry mulchers are an essential tool in the arsenal of sustainable land management. By leaving root systems in place, they preserve the environment by preventing erosion and allowing soil to remain healthy and regenerate.
In other fire-prone western states, including California, Forestry Mulchers are essential in producing defensible space and fire breaks. Many of these farmers and right-of-way managers find mulchers the easiest, quickest and most effective way to remove brush and invasive species.
They reduce the necessity of burning or extensive digging! These machines are equally essential for creating and maintaining access trails and stabilizing slopes after heavy storms or in the aftermath of wildfires.
Regional land management needs
- Pacific Northwest: Dense conifer forests, seasonal rainfall, steep slopes
- Southeast: Fast-growing brush, invasive species, clay-heavy soils
- Southwest: Arid climate, rocky ground, cactus and mesquite
- Midwest: Mixed hardwoods, prairie encroachment, wetland edges.
Regional land management needs Climate, soil, and vegetation density dictate mulcher choice. Versatile mulching attachments to shift as ground conditions and vegetation types change.
Pairing the right mulcher to the region’s unique clearing needs ensures optimal efficiency and machine longevity.
Matching mulcher type to terrain
- Drum mulchers for dense, heavy brush and large diameter trees
- Disc mulchers for fast, aggressive cutting in open areas
- Deck mulchers for lighter vegetation and flat grades.
Select attachments with specific flora and density in mind. Run your forestry mulcher where you plan to work.
Consider appropriate speed and capacity for challenging sites, and consider not overloading the machine to avoid damaging it. Choosing the right type of mulcher for the application keeps productivity levels high and repair costs low.
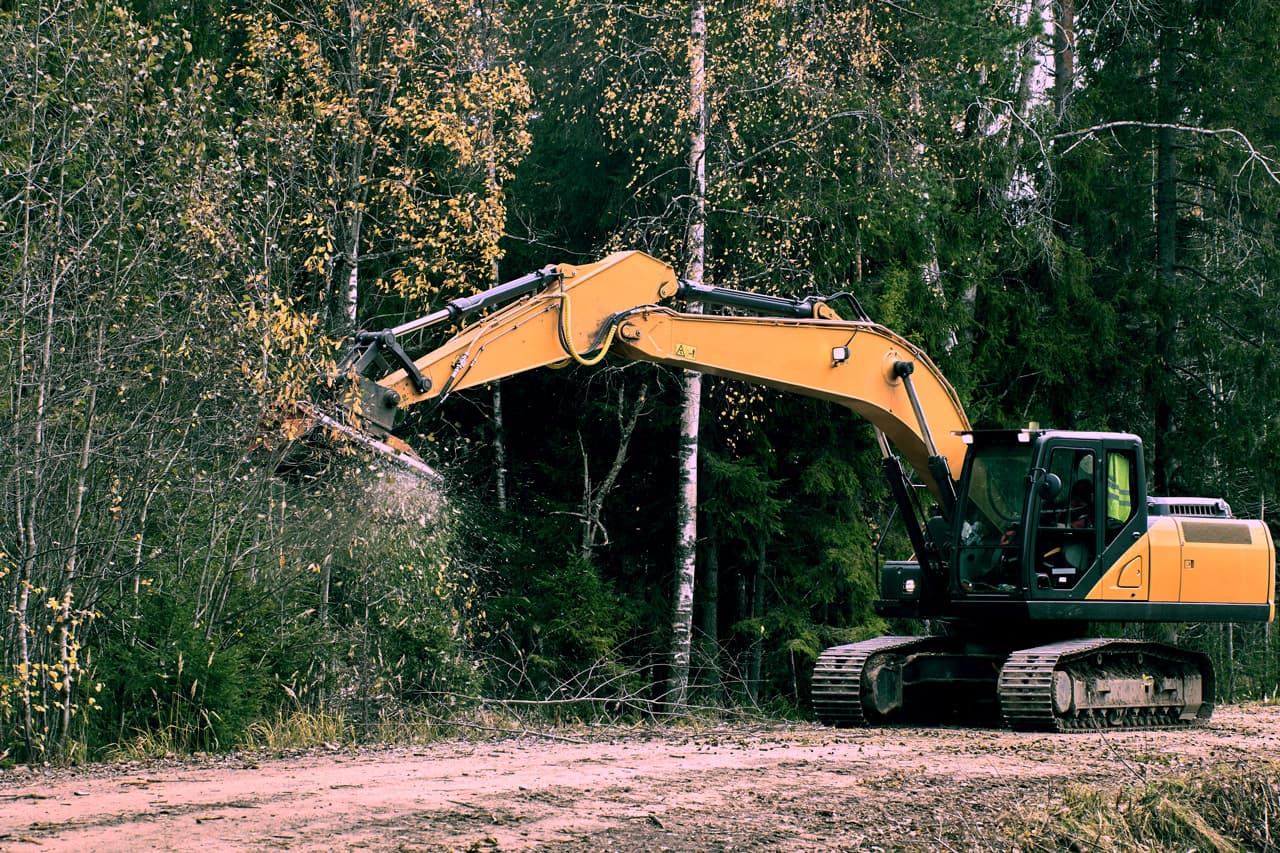
4 Signs your forestry mulcher needs replacement or upgrade
Knowing when your forestry mulcher needs replacement or an upgrade is imperative. This knowledge is essential to keeping you productive and safe as you work on land-clearing projects from the beaches of California to the forests of Washington state. Ignoring these early warning signs is a recipe for disaster.
Worn out cutting performance or frequent malfunctions result in unscheduled downtime and increased operational expenses. Consistent inspection and proactive maintenance are essential to keeping equipment running smoothly and avoiding costly breakdowns. Upgrading your forestry mulcher in a timely manner not only protects productivity, it keeps you in step with increasing safety regulations and provides better working conditions for your operators.
Symptom | Performance Impact | Cost Risk | Safety Impact | Project Impact |
---|---|---|---|---|
Declining Performance | Reduced mulch quality, slower pace | Fuel waste | Stress on operator | Delays, incomplete clearing |
Frequent Breakdowns | Unplanned stops, lost time | High repair bills | Increased hazards | Missed deadlines |
Rising Maintenance | Inconsistent output | Escalating spend | Distraction, fatigue | Budget overruns |
Outdated Safety | Limited protection, no sensors | Liability | Injury risk | Regulatory delays |
Project Mismatch | Inadequate capacity | Inefficiency | Strain, errors | Inability to scale |
1. Declining cutting performance
Dull blades, worn cutting teeth, and improper sharpening will inevitably result in a loss of efficiency in mulching. These problems are exacerbated with regular heavy use in challenging West Coast vegetation. As a result, operators might find there’s a more uneven distribution of mulch, reduced work pace and greater resistance when processing larger, thicker branches.
Having a record of changes in cutting capacity over time can provide evidence of a downward trend. A significant slowdown in your mulching speed or an increase in the amount of fuel you’re using is a clear sign that your mulcher needs replacing.
2. Frequent mechanical breakdowns
Mechanical reliability quickly deteriorates as components wear. Typical breakdowns involve loose hydraulic fittings, ongoing leaks, and irregular electrical failures. It is vital to frequently inspect all bearings, hoses, and belts.
Constant downtime or the need for repeated repairs could indicate an obsolete equipment design or lack of proper maintenance. For procurement teams, increased frequency of breakdowns is an easily defensible reason to invest in new equipment.
3. Outdated safety features
Today’s forestry mulchers come equipped with shrouds, guards, high-tech sensors, and ergonomic controls to reduce operator strain and increase safety. These features were not available on older models, which raises the risk of accidents and lowers compliance with today’s standards.
Operators are at greater risk and increased legal exposure when working with antiquated machinery. Consulting with your manufacturer’s bulletins will help you make sure you’re utilizing the latest safety features.
4. Inability to meet project demands
Project demands change over time. Signs of an incompatible mulcher are shallowing cutting depths, reduced throughput, or an inability to effectively process denser or more abrasive material.
Moving into tougher, more complex projects might mean you need more capacity—or more power. Evaluating attachment compatibility with new carrier models or upcoming project needs can spare you the aggravation of exacerbating kinks in your operation or schedule.
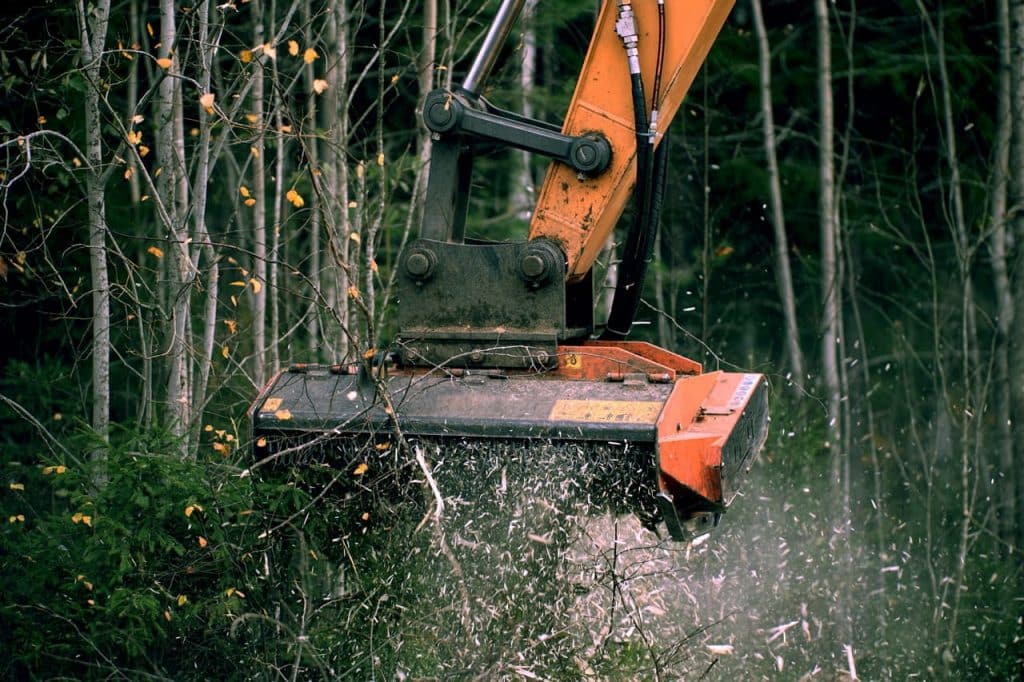
How to troubleshoot common mulcher issues
The key to successful troubleshooting starts with having a process to follow. Forestry mulchers, whether working the slopes of the Pacific Northwest or tackling dense chaparral near Los Angeles, demand daily attention to maintain operational standards.
A methodical way based on consistent monitoring and rapid response can keep contractors from losing time and money through unexpected outages and expensive service. By keeping a helpful troubleshooting checklist on hand, crews can quickly diagnose mulcher issues, keeping downtime and safety from being at risk.
Essential Troubleshooting Steps:
- Do a daily walk-around looking for leaks, damaged or worn hoses, and other visible damage.
- Check belt tension by pulling with 30–40 lbs of force. A deflection of about a half-inch would be perfect.
- Listen for abnormal sounds or vibrations during initial operation.
- Ensure that all lubrication points are properly lubricated according to the manufacturer’s recommendations.
- Preventative maintenance and attention to operation can go a long way in keeping your mulcher running smoothly.
Identify wear and tear early
A simple visual inspection of teeth, blades, and drum surfaces prior to each use can help identify where there is wear, cracks, or if any segments are missing. When your mulcher works inconsistently or starts making abnormal sounds, it’s usually a sign that something more serious is going on.
Keeping a record of wear patterns, like regular dull areas or inconsistent blade wear, allows you to order replacement equipment before you run out. Prompt repairs, such as replacing a broken tooth or tightening a few loose bolts, help maintain equipment for the long haul and avoid dangerous and costly equipment failure.
Check hydraulic system health
Hydraulic system health directly correlates to mulching output and operator safety. Routine checks of hoses, fittings and fluid reservoirs can catch leaks and signs of material degradation early on.
Check pressure and response in operation. Slow or erratic movement usually means internal wear. To maintain pressure ratings and prevent contamination, replace all damaged hoses or fittings with OEM-standard components. A healthy hydraulic system means steady-state work with less risk of unexpected downtime.
Inspect teeth and drum condition
Sharp, properly balanced teeth and drums ensure an even, consistent mulching. Inspect teeth and drum condition. Look for signs of dullness, chips, or missing teeth—uneven wear will cause excessive vibration and poor end product appearance.
Employ a tooth gauge for accurate measurement, and consider replacing worn units with high-quality forestry-grade replacements. During installation, double check fit and torque specifications. Taking this step will avoid early loosening or misalignment, turning small problems into expensive fixes.
Maintenance tips to extend mulcher life
Increasing the production life of a forestry mulcher working in the tough West Coast conditions takes more than just scheduled maintenance. A structured, regular maintenance program is key to dependable performance and years of return on investment. By incorporating consistent practices, selecting premium components, and maintaining thorough documentation, operators can achieve the highest levels of uptime while avoiding expensive repairs.
A robust maintenance program for forestry mulchers should include the following intervals:
- Daily: Inspect mulcher tools, teeth, and blades for wear. Clear all debris and organic build-up from all exposed surfaces. Inspect hydraulic hoses and fittings for leaks or damage. Check hammer bolt and fastener tightness.
- Weekly: Lubricate all specified moving parts, including bearings, joints, and drive chains. Sharpen or replace steel blades when they dull or wear. Use compressed air or water to clean areas that are difficult to reach.
- Monthly: Perform a comprehensive inspection of hydraulic systems. Check maintenance logs to verify regular part replacement and routine maintenance intervals. Audit the condition of high-wear components, when needed sourcing OEM parts to replace with the same quality.
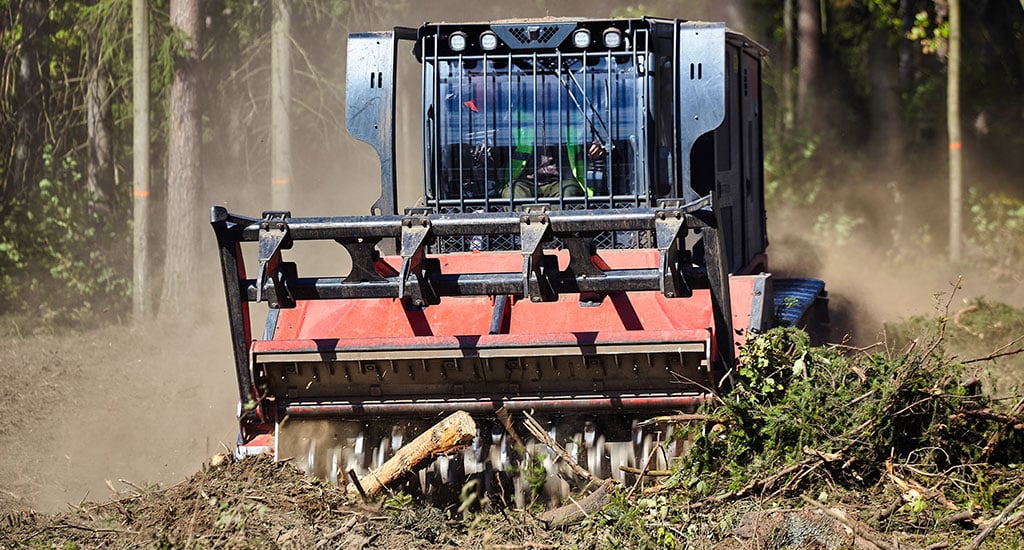
Clean after every use
At the end of each job, operators should remove any remaining debris, muck, and plant material from all exterior and internal surfaces. Compressed air or a pressure washer is the ideal way to keep the cutter head, bearings, and undercarriage clean.
As you’re cleaning, look for cracks, corrosion, or buildup not easily seen that may cause faster wear. Cleaning your mulcher after every use will lower your chances of corrosion and help keep all moving pieces in proper working order.
Lubricate moving parts regularly
Bearings, joints, and drive chain should be lubricated as per manufacturer instructions, never with grease, oil, or solvents not specified in the manual. Watch for dry areas, squeaking, or rubbing—indications of a lack of lubrication.
By lubricating moving parts accordingly, you will not only save on maintenance costs, but you’ll prolong the life of other high-value components.
Replace worn components promptly
Track a wear item checklist for teeth, blades and hammer bolts. Replacement whenever possible, use OEM replacement parts and components for the longest life and best results.
Create frequent opportunities to check for loose or malfunctioning parts, particularly during extended operating hours. To avoid larger breakdowns and expensive downtime, it’s important to replace worn components in a timely manner.
When to repair vs. replace
Deciding between repairing or replacing a forestry mulcher is a core challenge for many operators, especially in demanding West Coast forestry and land management environments. This decision goes far beyond just looking at first costs. It’s really about striking a balance between short-term repair needs and long-term operational objectives, taking into account machine age, usage history, and the role of emerging technologies.
Robust maintenance programs and the creation of preservation and inspection histories provide valuable information that should inform these decisions.
Assess total cost of ownership
Consider the whole cost—not just the expected repair invoice. This includes registering the total cost of ownership including purchase price, maintenance costs, repair history with frequency and costs, as well as downtime consequences.
For instance, an old mulcher may require repairs on its hydraulic system every few months. At $7,000 per annual repair, the cumulative amount would soon exceed 50-70% of a new unit’s price. Calculate all these variables relative to projected life cycle and equipment performance.
Many operators find upgrading to modern, fuel-efficient units with advanced cutting heads can lower maintenance costs and extend operational life. Creating a summary cost table makes these decisions easy for procurement teams.
Evaluate downtime impact
Consider the impact downtime has aside from missed trip time. Meanwhile, increased project delays increase labor costs and expose contractors to risk of contract penalties.
If a mulcher is constantly down, measure the time lost and contracts not met—these can add up to a replacement being a better investment before long. For effective management of California or Oregon forests, equipment uptime is a key decision-making metric.
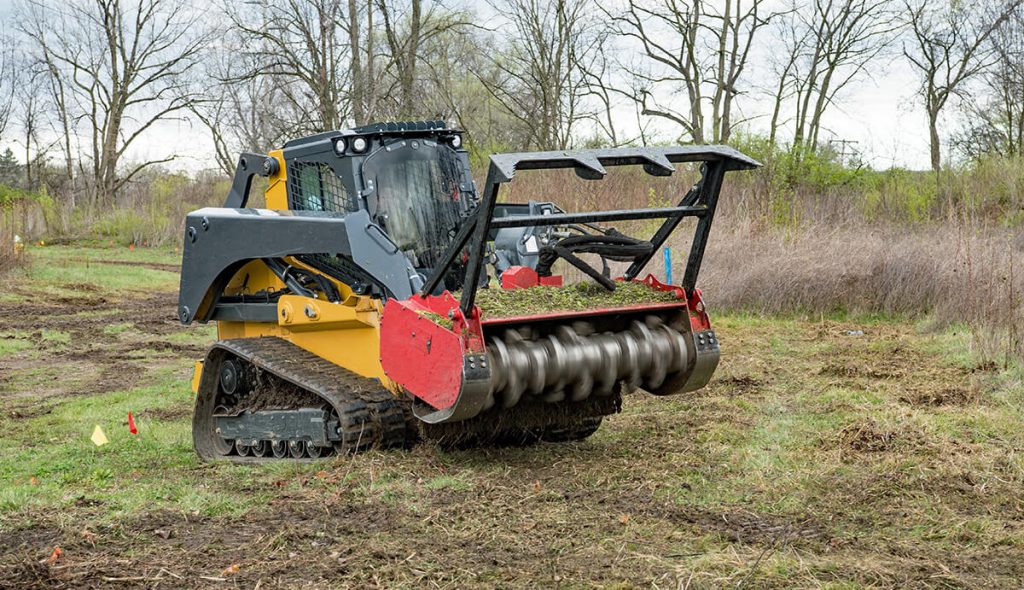
Choosing the right mulcher for your needs
Choosing a forestry mulcher isn’t just a purchase, it’s an investment in fit-for-purpose solutions that align with your operational realities. Land-clearing requirements on the West Coast are all over the map. For instance, they can add in fire mitigation in chaparral and utility corridor maintenance in mixed conifer areas.
Choosing between drum, disc and deck mulchers comes down to the size of your projects, the type of vegetation you’ll be working with and your budget. The following table summarizes key differences:
Mulcher Type | Project Scale | Vegetation Type | Budget |
---|---|---|---|
Drum (Fixed Tooth) | Large, High-Frequency | Dense brush, hardwood | $$$ |
Disc | Medium-Large | Mixed saplings, small trees | $$ |
Deck | Small-Medium | Grass, light brush | $ |
Understand project scale and frequency
First, consider your operating tempo. Extensive or frequent roadside clearing usually requires a high-production, heavy-duty drum mulcher, designed for high-volume and wear. For smaller, urban infill projects or periodic lot clearing, a compact deck mulcher can be more efficient, offering nimble maneuverability and reduced fuel costs.
Ensure the mulcher’s hydraulic capacity is compatible with your carrier’s flow. You will get the best performance when you are working in the top half of the rated flow range!
Factor in local vegetation types
Consider the types of vegetation you’re dealing with. Treatments for madrone, tanoak, or invasive species like Scotch broom sometimes require more specific tools. For heavy, constant cutting, they need carbide teeth or depth-control drums.
If you need to work specifically in grasslands or scrub, then a deck mulcher will get the job done. Refer to local vegetation maps or speak with local forestry consultants to prepare for specific biome obstacles.
Our expert opinions and personal insights
Choosing the most appropriate time to upgrade or replace forestry mulchers requires going beyond initial manufacturer recommendations. Daily field realities and operator feedback drive this innovation. It is further shaped by changing land management objectives throughout the West Coast and greater Pacific.
A mixture of scientific precision and real-world experience fosters winning results. This is particularly important when taxpayer dollars and years of project time are at stake. Below, insights from experienced professionals and engineers clarify practical strategies and common pitfalls, with actionable lessons for keeping operations running strong.
Lessons learned from field experience
As our members have told us, operators know that if they want to avoid costly failures, routine daily inspections are a must. Debris accumulation, hydraulic leaks, and worn teeth are the leading offenders—catching these early prevents machines from being down and out.
Implementing regular end-of-season maintenance checks, along with regular in-season maintenance practices, prolongs the life of your equipment and prevents unexpected downtime. Most teams are already familiar with digital logs that log service intervals and part replacements.
Providing operators with continuous and high-quality training improves safety and performance. Crews that know the right cutting speeds and mulcher settings find they complete the job more smoothly with fewer breakdowns.
In the demanding field environment, troubleshooting often comes down to replacing time-worn parts. It means recalibrating hydraulic flow—skills developed through the field, not just the textbook.
Mistakes to avoid when upgrading
Even failing to account for the scale of land clearing work underestimated the wear on equipment and led to premature failure. Never assume mulcher specs will handle the intended vegetation or terrain.
Saving short-term by selecting the lowest-cost replacement parts almost always leads to increased repair frequency and downtime. Failing to consider machine compatibility or operator safety measures when upgrading can lead to hazards and inefficiencies.
A thoughtful review of new improvements, from mower decks to electronic controls, guarantees that improvements meet real needs.
Need support with maintenance, troubleshooting, or repairs? Get in touch with SpiderMax — our team responds promptly and ensures every intervention is carried out to the highest standards. All repairs are backed by original OEM parts for guaranteed reliability.